Comment by Composite Analytica on 18 Apr 2011 at 11:23:44

|

|responses: 5|
Dear Jonathan,
In this case the diffusion coefficient seemingly decreases, with an increase of concentration of carbon dioxide in the elastomer membrane. This is the opposite of what normally happens with plasticizing and swelling: an increase of the diffusivity (or decrease of the mutual friction coefficient) as function of the permeant concentration.
From various rubbers this is known to happen with molecules like Water and CO2. These molecules cause a better ordening and dipole-dipole / hydrogen bonding in the chain structure of these rubbers.
Mind that filler particles do also influence the diffusion rate and the solubility of small molecules in elastomers and rubbers. From carbon fillers it is known that they cause accumulation of molecules such as helium, hydrogen, nitrogen, carbon dioxide and water around their internal surface. This diffusion with simultaneous accumulation, causes a decrease in overall diffusion rate and an increase in solubility.
Maybe you could provide us with some more specific information, such as the laboratory test results - carbon dioxide pressure build-up as a function of time, partial pressure and thickness of poly dimethyl siloxane polymer.
By the way: mind that for carbon dioxide and flue gas scrubbing or transport Sulfonated Polyether Etherketone (S - PEEK) is also an option (probably an issue because of global warming, world wide reduction of carbon dioxide exhaust). For pipeline coating purposes an epoxy would probably be a good solution.
Regards,
Composite Analytica
Comment by don bobo on 02 May 2014 at 23:35:34

|

|responses: 0|
We are trying to calculate the dimensions, diameter and length, of a cylinder that will limit CO2 flow to 1 cc/minute with a CO2 source pressure of 800 psi (~4000 cm Hg) The gas will exit into 1 atm. We would like the diameter to be something about 4 to 8 mm.
I understand that the high pressure will reduce permeability, but at this point an educated guess would be fine as the real number will be found through experimentation
If this is a simple calculation for you, I'd appreciate it if you would send the dimensions we should start with in our experimentation. If it's a more time consuming task, please send me a quote on doing the job.
Regards
Don Bobo
Comment by Jonathan on 05 May 2011 at 10:12:38

|

|responses: 3|
See the graph of mass transfer as function of time for CO2 in PDMS below:
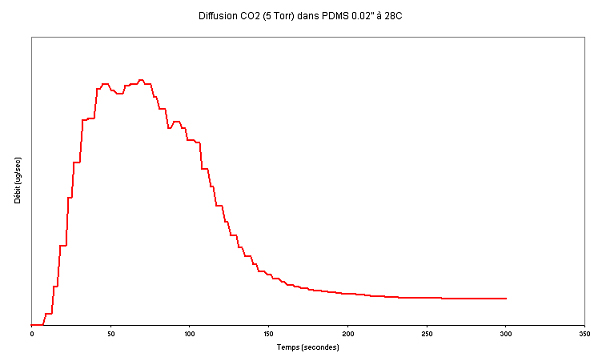
For the pressure and the thickness:
5 torr = 5 mm Hg
2"(inch) = 508 micro meter
The membrane surface is 10,21 cm^2
We test three membranes of differents thickness (280, 508 and 970 micro meter). The same behavior occurs with differents thickness. But thicker is the membrane higher the feed pressure must be to see the strange behavior.
Comment by Composite Analytica on 27 May 2011 at 16:17:24

|

|responses: 2|
Jonathan,
From the graph it becomes obvious that it is a case of decreasing diffusivity with increasing Carbon Dioxide concentration (actvity) in PDMS. This is also described in for polar molecules in Cranck's Diffusion in Polymers (1969), on page 301, Water in PDMS. Module 102 of CheFEM (the module for chemical activity and surface corrosion driven adjustments of diffusion) can deal with this type of process.
Regards,
Composite Analytica
Comment by David on 02 Oct 2012 at 23:53:13

|

|responses: 0|
Dear Composite Analytica,
You mention that epoxy might be a good solution to resist carbon dioxide diffusion. Can you tell me where I might find diffusivity of CO2 through epoxy?
Regards,
David
Comment by Jonathan on 07 Jun 2011 at 21:22:15

|

|responses: 0|